Innovative Methods
The MCL has an extensive range of characterisation methods and expertise in process technology for manufacturing electronic components at its disposal. The main activities lie in the coupling of simulation and modeling with experimental analysis. This enables fast method development and in depth analysis of results.
Our methods cover structure-property relations, non destructive testing using ultrasound. Furthermore, the MCL offers a variety of testing methods to characterise the durability of electronic components. The focus lies on identifying the thermal, electrical and mechanical properties of components and their constituent materials. With the aid of advanced numerical simulation, we close the circle between function assessment, reliability assessment and predictive reliability analysis.
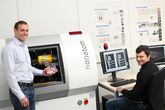
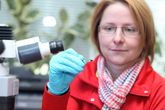
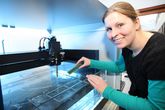
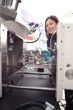
In-situ-Characterization of Structure-Property Relations
Structure property relations are the basis for understanding material properties under loading conditions. This broad topic at the MCL can be exemplified with a recent project. Together with researchers from North Carolina State University and from University of Leoben, the MCL is working on structure-property-relations of piezo-ceramics. These ceramics intrinsically are capable to transfer mechanical stimuli to electric signals and vice versa, a property which enables a very broad range of applications in acting (e.g. nano-positioning) and sensing (e.g. vibration sensors). The material behaviour is investigated using high energy ex-ray diffraction while coupled mechanical and electrical load is applied. XRD allows for simultaneous characterization of stress, texture and phase while external load is applied and therefore a nearly full image of the influence of microstructure on function is gained.
This allowed to study the influence of applied load on the texture, which is known to have a large influence on the properties inside of the material. It was found that a one-time overload chances permanently the possibility of reorientation. With the same data it was possible to quantify the influence of texture on stress strain hysteresis. Using this information, new materials can be developed and the application scenarios can be improved.
Contact: Marco Deluca
Advanced Non-Destructive Testing
The characterization of elastic material's properties in thin film systems or the non-destructive identification of failure modes in highly complicated 3D integrated structures or modern print circuit boards (PCBs) with respect to “rapid learning” represents a demanding challenge in microelectronics. Ultrasound waves are a highly efficient possibility for the non-destructive characterization of material properties and failures in microelectronics. Here, image as well as non-image based methods can be used.
Examples are scanning acoustic microscopy (SAM) or laser induced ultrasound (LUS), respectively. The MCL develops in collaboration with partners e.g. PVATepla, Fraunhofer IMWS, and the Imec novel measurement and analysis approaches which are based on the SAM method. In addition, novel concepts for non-contact characterization of material parameters using laser induced ultrasound are developed in collaboration with the University of Graz. The goal is to provide accurate process attendant failure and material characterization.
The analysis of complex and small geometries used in e.g. microelectronics or modern energy storage systems is highly demanding. Here, tomography based methods like X-Ray computed tomography (XCT), FIB-tomography etc. represent highly useful tools. However, the analysis of the obtained 3D data to gain accurate information is an obstacle due to reconstruction problems, measurement artefacts, limited resolution, and contrast. In order to meet these challenges the MCL develops algorithms for demanding segmentation problems, applies commercial available state of the art software packages and uses tomography based methods to produce reliable data. In addition, the MCL uses data meshing approaches where 3D & 2D image data is linked to numerical simulations like CFD and FEM to provide simulations on realistic samples. The overall goal is to provide a comprehensive, extensive, fast, and reliable information regarding structural properties for material engineering.
Contact: Roland Brunner
Reliability Research and Test Development
The coupling of simulation and experiment is the basis for the development of reliability tests at the MCL. Especially for components with a very long lifetime the prediction is very complicated, time consuming and expensive.
High power light emitting diode (LED) has gained more and more importance over the last decade as a long-life general illumination source. To ensure a long-lasting lifetime of the LED module, knowledge about critical failure modes has to be generated. However, it is extremely time consuming and complicated to assess the failure mechanisms and the reliability of the whole LED system.
At the MCL, a universal method for the design of tests was established and successfully exemplified on LED modules. We investigated an accelerated test method based on a dynamic mechanical analyser (DMA) to transfer the time-consuming electrical switching test (SST) into a fast, purely thermo-mechanical one (ATMT). The electrically induced thermo-mechanical stress levels due to switching cycles are modeled with experimentally validated finite element multiphysics simulations to compare thermally induced strains and stresses with equivalent, purely mechanical stresses causing similar strain/stress scenarios.
This result of the simulation was transferred into an experimental setup that consisted of a DMA. There, deformation was applied by a compression tool mimicking the thermal expansion of the silicone and consequently leading to similar failures as observed in the SST test.
The occurred failure modes and the comparable number of cycles until failure represent the possibility to replace the SST with the ATMT in the future. These findings can be considered as a further step for the development of an alternative accelerated testing procedure based on thermo-mechanical fatigue for replacement of traditional standards.
Contact: Elke Kraker